Энергоемкость украинской экономики — самая высокая в Европе
Металургія 25.04.2014 08:50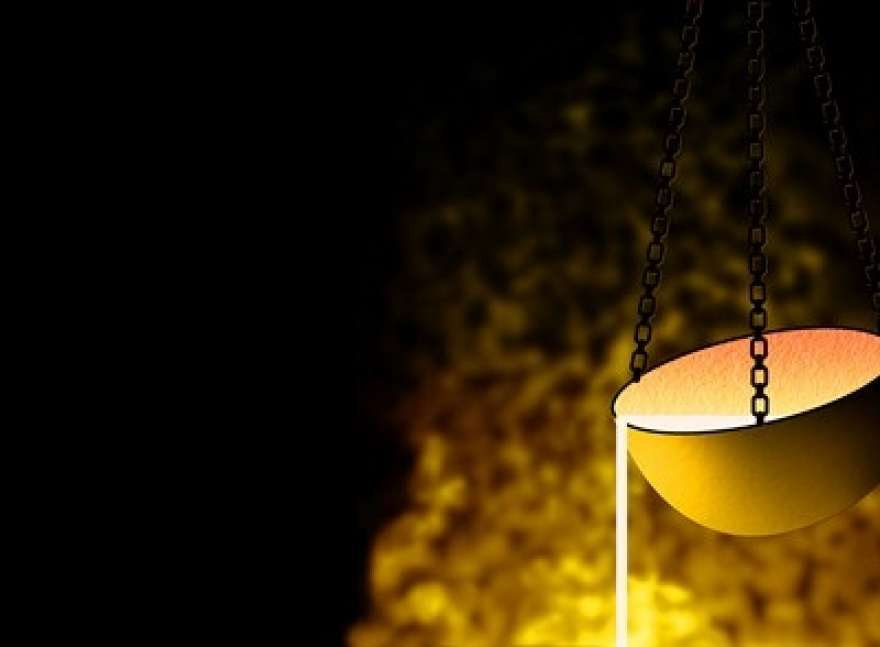
Несмотря на то что с 2001 по 2011 г. энергоемкость отечественной экономики сократилась на треть, Украина значительно опережает по этому показателю развитые страны. В частности, в 2010 г. на $ 1 тыс. произведенной в нашей стране продукции расходовалось 0,55 т условного топлива (за единицу у. т. принимается теплотворная способность тонны каменного угля), тогда как в соседней России этот параметр составляет 0,44 т у. т., Чехии — 0,22, Польше — 0,19, Германии — 0,15.
Повысить энергоэффективность украинской индустрии — это и модернизировать саму энергетическую систему, одну из самых отсталых в Европе, и заменить дорогой импортный газ на более дешевые энергоносители. Напомним, ежегодное потребление природного газа в металлургии и химии составляет 16‑17 млрд куб. м в год. Это половина того, что закупала НАК «Нафтогаз України» последнее время в России. Этот газ обходится отечественным сталеварам и химикам довольно дорого, поэтому, когда говорят о снижении энергозависимости Украины, как правило, вспоминают именно эти отрасли. Но ответ на вопрос, как сократить потребление газа в этих сферах, принципиально отличается. Ведь для химиков газ — это в первую очередь сырье, а для металлургов — топливо для поддержки технологических процессов.
Больше углей
Для металлургов остается актуальным вопрос избавления от газовой зависимости, ведь стоимость голубого топлива в себестоимости их продукции достигает 10 %. По словам начальника аналитического отдела государственного предприятия «Укрпромвнешэкспертиза» Павла Перконоса, в мировой металлургической индустрии направление энергосбережения предусматривает внедрение нескольких технологий, которые позволяют сократить потребление природного газа и электроэнергии. Первая — внедрение так называемой технологии вдувания пылеугольного топлива (ПУТ). Она предусматривает сокращение расхода природного газа за счет замены его пылеугольным топливом при производстве чугуна. В Украине такая технология уже внедрена на «Донецкстали», Алчевском металлургическом комбинате, «Запорожстали» и ММК им. Ильича. Также планируется запуск на Днепровском меткомбинате им. Дзержинского и Енакиевском МК. В среднем эта технология, по оценкам металлургов, требует от $ 40 млн до $ 120 млн для каждого метпредприятия и окупается в течение двух-трех лет.
«Если традиционно на выпуск тонны чугуна расходуется около 100 куб. м газа, то при использовании ПУТ потребность в топливе снижается до 20 кубометров на тонну», — говорит Перконос. В то же время потребность собственно в ПУТ составляет около 150 кг на тонну чугуна. В результате, по данным эксперта, вдувание пылеугольного топлива позволяет существенно экономить на газовых затратах при производстве заготовки. Например, при отсутствии технологии ПУТ доля газа в себестоимости тонны заготовки оценивается в 9,7 %, а при наличии соответствующих установок сокращается до 3,1 %. «В настоящее время внедрение ПУТ снова актуально для металлургов. По нашим расчетам, цена природного газа на уровне $ 480 за тыс. куб. м на границе обернется для отрасли ростом затрат на тонну продукции на $ 15 в том случае, если ПУТ не применяется», — отмечает Перконос.
Согласно подсчетам «Укркокса» и «Металлургпрома, чтобы перевести все доменное производство на технологию ПУТ, металлургам понадобится до 15 млн т качественных коксующихся углей в год. «Для этой технологии нужен кокс повышенного качества. К сожалению, из необходимого нам коксующегося угля украинские шахты могут обеспечить только треть», — сетует генеральный директор «Укркокса» Анатолий Старовойт. По его словам, именно поэтому Минэнерго Украины приняло решение пока не квотировать импорт коксующегося угля.
За счет внедрения на металлургических предприятиях ПУТ экономия природного газа составит 3 млрд кубометров.
Как еще экономить
Сталевары могут экономить электричество, используя газы, выделяющиеся при производстве чугуна и стали. Внедрение так называемых когенерационных установок позволяет перерабатывать доменный, коксовый и конвертерный газы, выделяемые в ходе производства, в электроэнергию, указал Перконос. Кроме того, подобное оборудование способствует сокращению вредных выбросов в окружающую среду. Когенерационная установка в Украине была запущена пока только на Алчевском меткомбинате корпорации ИСД в 2013 г. Общая стоимость проекта составляла $ 383 млн, из которых $ 120 млн предоставил Японский банк международного сотрудничества. Еще $ 150 млн дал предприятию Европейский банк реконструкции и развития, $ 50 млн — Calyon Bank. В результате меткомбинат смонтировал установку мощностью 303 МВт, что сравнимо с потребностями в электроэнергии, например, Полтавской области. Алчевскому меткомбинату установка позволит сократить выбросы углерода на 7 млн т, что соответствует годовому объему выбросов такого промышленного города, как Манчестер.
Улучшение старого
В себестоимости украинской химической продукции газ достигает 40‑70 %. Химики сегодня не могут его вытеснить (хотя в свое время обходились вовсе без газа), поэтому стремятся внедрять современные технологии, позволяющие модернизировать работающие агрегаты по выпуску аммиака, карбамида и селитры, снижать затраты энергии и углеводородного сырья в процессе их производства. «Способов много, смотря какая цель. Можно предельно уменьшить расход газа и электричества на производимую тонну продукции, а можно нарастить выпуск продукции, сократив общие энергозатраты», — рассказывает «Капиталу» технический директор одного из заводов OSTCHEM Дмитрия Фирташа. От масштаба экономии зависят инвестиции и конечный результат.
Самым «газоемким» продуктом у химиков является аммиак. Собственно, и экономия в азотном производстве начинается с аммиака как исходного сырья для производства других удобрений. Средний расход газа на выпуск тонны аммиака в Евросоюзе колеблется в пределах 900‑950 куб. м, говорит собеседник. «Средний расход газа на украинских предприятиях составляет 1080‑1150 куб. м на т аммиака. Наилучшие показатели экономии — на Одесском припортовом заводе (ОПЗ) и черкасском «Азоте». Там и газа расходуется меньше, и выпуск продукции вырос после реконструкции на 20 % и более», — подтвердил технический директор. А вот новые производства аммиака, которые запускают преимущественно страны Ближнего Востока, где есть крупные запасы газа и нефти, имеют коэффициент расхода газа уже на уровне 750‑800 куб. м на т аммиака, но стоимость такого оборудования исчисляется миллиардами долларов. За арабскими химиками нам не угнаться, потому что они быстро окупают новые проекты благодаря доступу к собственному дешевому газу, который им обходится примерно в $ 40‑50 за тыс. куб. м против нашей стоимости — $ 400 и выше за тыс. кубометров.
Реконструкция старых агрегатов гораздо дешевле и быстрее окупается. «Мы, например, израсходовали на модернизацию своего агрегата аммиака $ 55 млн и результатом довольны — расход газа снижен с 1250 до 993 куб. м на т», — рассказывает техдиректор химпредприятия.
Если учесть, что в Украине 15 работающих агрегатов аммиака на 6 предприятиях, только их модернизация требует от инвесторов свыше $ 800 млн. Некоторые из них уже модернизированы, а именно на трех предприятиях — ОПЗ, черкасском «Азоте» и «Рівнеазоті». Насколько продвинулась реконструкция остальных агрегатов аммиака — судить трудно (официальных данных никто не обнародует), но если учесть, что средний расход газа на химпредприятиях Украины составил в 2013 г. 1150 куб. м газа на т аммиака, то экономия на каждом агрегате достигает уже около 250 куб. м газа в сравнении с изначальными расходными коэффициентами.
Если верить последним данным, то азотные предприятия за последние пять лет снизили потребление природного газа с 7,5‑8 млрд куб. м до 6 млрд, или на 1,5‑2 млрд кубов. Но следует учитывать также тот факт, что с начала кризиса, с 2009 г. и по сегодняшний день, химики не каждый год загружают производства на полную мощность, что также влияет на расход газа.
Энергоэффективная энергетика
Главная проблема украинской энергетики — износ мощностей: в основном энергоблоки отечественных теплоэлектростанций (ТЭС) общей мощностью 33,8 ГВт были построены еще в 1960‑1980 гг. С 1980 по 1990 г. было введено в строй только 14,9 ГВт мощностей ТЭС. Моложе в этой подотрасли активов нет. Износ отечественной тепловой генерации достигает более 73 %, и на начало этого года многие ТЭС пересекли признанную в мировой энергетической практике черту граничного ресурса и физического износа в 170 и 200 тыс. часов соответственно.
Энергохолдинг ДТЭК — основной производитель украинской электроэнергии на тепловых станциях — заявил, что от точечных проектов перешел к системной программе повышения эффективности. За последние два года компания инвестировала 4,2 млрд грн в реконструкцию и энергомодернизацию предприятий. В результате ДТЭК сэкономил 236,4 млн кВт·ч электроэнергии в 2012‑2013 гг., или 314,5 млн грн в денежном выражении.
Основные средства холдинг вложил в сферу генерации электроэнергии: с 2008 г. было инвестировано 4,8 млрд грн в модернизацию 13 энергоблоков ТЭС. В 2014 г. ДТЭК планирует модернизировать более 20 энергоблоков. Проводимая модернизация энергоблоков дала украинской энергосистеме дополнительные 250 МВт мощности, что практически соответствует мощности одного дополнительного энергоблока ТЭС. Целевые программы по энергоэффективности и энергосбережению предусматривают, что с их помощью до 2016 г. ДТЭК будет экономить около 120 млн грн ежегодно.
Другие тоже могут
Остальные энергокомпании также заняты реконструкцией своих мощностей. В частности, в январе нынешнего года Кабинет министров утвердил технико-экономическое обоснование реконструкции блока № 1 Змиевской ТЭС компании «Центрэнерго» стоимостью 810 млн грн. Помимо увеличения установленной мощности блока с 175 МВт до 215 МВт, эта реконструкция позволит обеспечить сжигание низкореакционного угля без использования газа или мазута.
Третья по величине компания в тепловой генерации — «Донбассэнерго», эксплуатирующая Славянскую и Старобешевскую ТЭС, — с 2012 г. реализует комплексную программу модернизации мощностей, рассчитанную до 2025 г. Кроме увеличения установленной мощности ТЭС с 2795 МВт до 3635 МВт, будет также снижен расход топлива.
На Старобешевской ТЭС компания «Донбассэнерго» в 2011 г. в ходе реконструкции блока № 4 первой в Украине внедрила технологию сжигания топлива в циркулирующем кипящем слое. Самый масштабный проект на «Донбассэнерго» — реконструкция блока № 6 Славянской ТЭС стоимостью 6,8 млрд грн — планируется завершить в 2018 г. Всего до 2020 г. «Донбассэнерго» намерена направить на выполнение инновационных проектов и техническое перевооружение своих ТЭС более 10 млрд грн.
Миллиардные инвестиции
По подсчетам экспертов Государственного информационно-аналитического центра мониторинга внешних товарных рынков («Держзовнішінформ»), Украине для достижения уровня Чехии по энергоемкости понадобится $ 24 млрд инвестиций. В то же время, по оценкам «Держзовнішінформу», инвесторы рискуют вкладывать в проекты по энергосбережению деньги лишь в том случае, если получают гарантии их быстрого возврата — бизнесменов не привлекают проекты со сроком окупаемости более семи лет. При реализации более долгосрочных программ они требуют участия государства в виде финансирования или предоставления госгарантий.
Власти, особенно в нынешней ситуации, уповают главным образом на международное финансирование, но его размеры тоже не безграничны. Например, недавно вице-премьер-министр Украины по региональной политике, министр региональной политики, строительства и жилищно-коммунального хозяйства Владимир Гройсман заявил, что на внедрение в Украине проектов по энергоэффективности будет привлечено более $ 3 млрд внешних инвестиций. Среди этих проектов — программы Всемирного банка на $ 332 млн по модернизации поставок тепла.
Программы энергоэффективности внедряет и Агентство США по международному развитию (USAID). Его проект «Муниципальная энергетическая реформа в Украине», который планируется реализовать в 17 украинских городах, позволит за четыре года сэкономить примерно 270 млн куб. м газа и привлечь около $ 200 млн кредитов.
Теги: Донецксталь Запорожсталь Алчевский металлургический комбинат Укрпромвнешэкспертиза Енакиевский МК Переглядів: 2832